陶器文化历史悠久,在新石器时代就已初见简单粗糙的陶器制品。陶瓷的发明更是人类最早利用化学变化改变天然性质的开端,是人类社会由旧石器时代发展到新石器时代的标志之一。
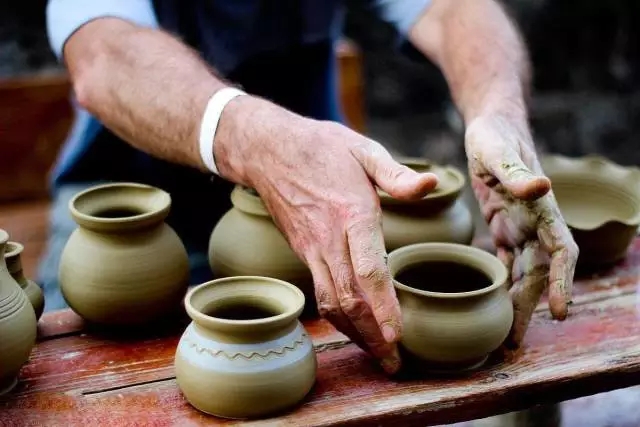
硬而脆的特点使陶瓷材料加工成型尤其困难,传统陶瓷制备工艺只能制造简单三维形状的产品,而且成本高、周期长。陶瓷3D打印技术的发展使复杂陶瓷产品制作成为可能,3D打印技术所具有的操作简单、速度快、精度高等优点给陶瓷注入了新的活力。
陶瓷3D打印市场发展潜力巨大
据知名市场研究公司MARKETS AND
MARKETS(M&M)发布的一份调查报告显示,3D打印陶瓷市场的全球规模有望从2016年的2780万美元增长至2021年的1.315亿美元,期间的复合年增长率(CAGR)将高达29.6%。该报告还显示,截至目前,3D打印陶瓷市场份额最大的地区仍是北美,并有望继续领跑;欧洲其次,而亚太地区则有望后来居上,在未来5年里坐拥全球最高的增长率。主要包含3D打印用陶瓷粉末材料市场、3D打印陶瓷产品市场和相关设备、技术市场等的陶瓷3D打印市场,发展潜力巨大。
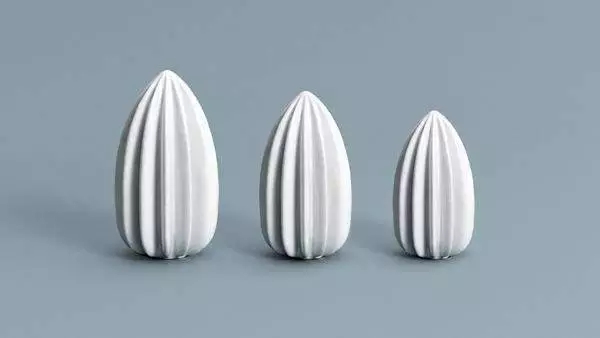
陶瓷的应用领域非常广泛,涵盖科研、医疗、工业、建筑及首饰等,尤其是具有许多有利性能的高级陶瓷材料更是航空航天及国防等领域需要的材料,而3D打印的陶瓷产品能保证良好的表面质量及各种良好性能。近日,科技部发布的《“十三五”先进制造技术领域科技创新专项规划》指出,强化制造核心基础件和智能制造关键基础技术,在增材制造、激光制造等领域掌握一批具有自主知识产权的核心关键技术与装备产品,形成以互联网为代表的信息技术与制造业深度融合的创新发展模式,促进制造业创新发展,以推进智能制造为方向,强化制造基础能力,提高综合集成水平,促进产业转型升级,实现制造业由大变强的跨越。
陶瓷3D打印成型技术
目前陶瓷3D打印成型技术主要可以分为喷墨打印技术(ink-jet
printing,IJP)、熔融沉淀技术(fuseddepositionmodeling,FDM)、分层实体制造技术(laminatedobjectmanufacturing,LOM)、选择性激光烧结技术(selectivelasersintering,SLS)
和立体光固化技术(stereolithography apparatus,SLA)。
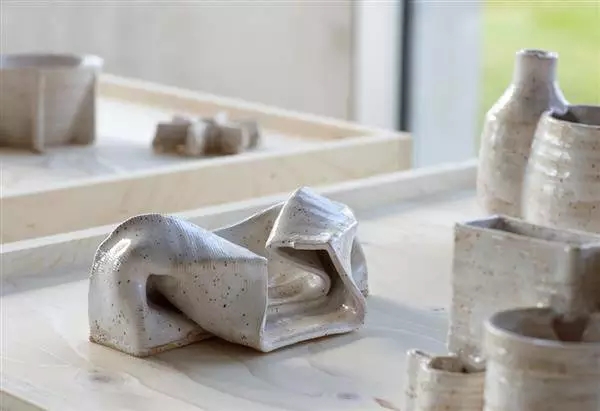
使用这些技术打印得到的陶瓷坯体经过高温脱脂和烧结后便可得到陶瓷零件。根据成型方法和使用原料的不同,每种打印技术都有自己的优缺点,发展程度也有差距。
01喷墨打印技术(IJP)
喷墨打印技术主要分为三维打印和喷墨沉积法。
三维打印是由MIT开发出来的,首先将粉末铺在工作台上,通过喷嘴把粘结剂喷到选定的区域,将粉末粘结在一起,形成一个层,而后,工作台下降,填粉后重复上述过程直至做出整个部件。所用的粘结剂有硅胶、高分子粘结剂等。三维打印法可以方便地控制陶瓷坯体的成分和显微结构,但是坯体需要后处理,而且精度低、强度低。
喷墨沉积法是由Brunel大学的Evans和Edirisingle研制出来的,它是将含有纳米陶瓷粉的悬浮液直接由喷嘴喷出以沉积成陶瓷件。该工艺的关键是配置出分散均匀的陶瓷悬浮液,目前使用的陶瓷材料有ZrO2、TiO2、Al2O3等。制约其发展的因素主要是陶瓷墨水的配置和喷墨打印头的堵塞。
02浆料挤出成型技术(类似FDM)
与塑料3D打印的熔融沉积成型(FDM)类似,基本都是由供料辊、导向套和喷头3个结构组件相互搭配来实现。首先热熔性丝状材料(混有陶瓷粉末的喷丝)经过供料辊,在从动辊和主动辊的配合作用下进入导向套,利用导向套的低摩擦性质使得丝状材料精准连续地进入喷头。材料在喷头内加热熔化后挤出喷嘴,挤出后的陶瓷高分子复合材料因为温差而凝固,按照设计好的原件造型进行3D打印。
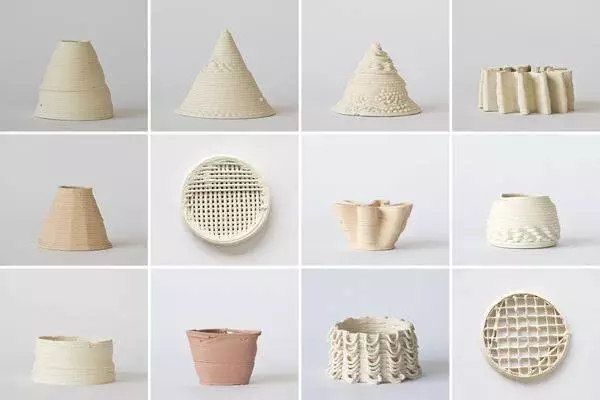
也有部分工艺采用高粘度的陶瓷浆料作为原材料,直接通过喷嘴挤出后在空气中干燥固化。
本技术虽然可以实现多种材料组合,但挤出最小直径有限,在结构上受到局限,精度较低,比较适用于陶瓷工艺品和多孔材料的生物制造领域。而且需要设置支撑结构、喷头温度高,对于原料的要求高。
03分层实体制造技术(LOM)
一种薄片材料叠加工艺,又称为薄形材料选择性切割。直接通过激光切割薄膜材料(含粘结剂),移动升降工作台,切割新的一层薄膜材料叠加在之前的一层材料上,在热粘压部件的作用下粘结成型,是一种直接由层到立体零件的过程。
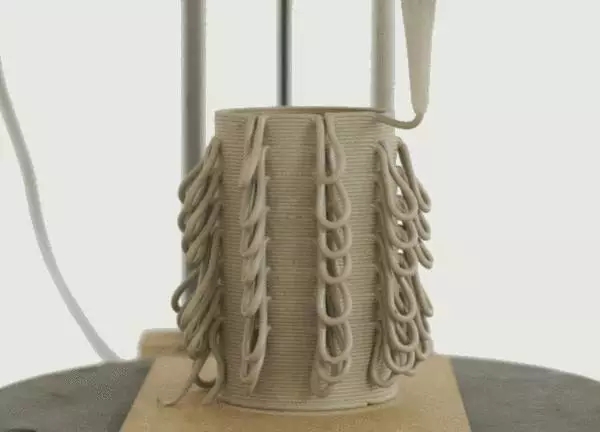
成型速度快,适合用于制造层状复杂结构零件;不需要设置支撑结构,后期处理过程比较简单。陶瓷薄片材料可以利用流延法制备得到,国内外对流延法制备陶瓷薄片材料的技术也已经比较成熟,原料的获取方便快捷。但是,由于采用的薄膜材料需要进行切割叠加,不可避免地产生大量材料浪费的现象,利用率有待提高。同时打印过程采用的激光切割增加了打印成本。不适合打印复杂、中空的零件,层与层之间存在较为明显的台阶效应,最终成品的边界需要进行抛光打磨处理。
04激光选区烧结技术(SLS)
主要通过压辊、激光器、工作台3个结构组件相互搭配来实现陶瓷3D打印。通过压辊将粉末铺在工作台上,电脑控制激光束扫描规定范围的粉末,粉末中的粘结剂经激光扫描熔化,形成层状结构。扫描结束后,工作台下降,压辊铺上一层新的粉末,经激光再次扫描,与之前一层已固化的片状陶瓷粘结,反复操作同一步骤,最终打印出成品。
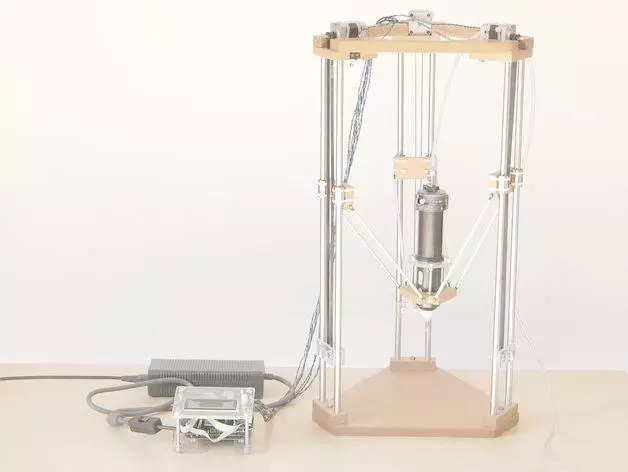
由于直接对陶瓷进行烧结比较困难,需在陶瓷粉中加入粘结剂或者将原料制成覆膜陶瓷的结构。粘结剂的种类、用量以及加入粘结剂后的陶瓷密度低、力学性能差等方面的问题一直制约着该技术的发展,难以得到高精度、高强度、高致密度的陶瓷零件。同时,由于使用激光,该技术打印陶瓷零件成本高、后期维护较为繁琐。
05立体光刻技术(SLA)
又称光固化成型技术。根据光源种类及作用方式的不同,分为激光扫描固化(SLA)和DLP(Digital Light Processing,数字光处理)面固化工艺。
SLA技术是通过激光的扫描曝光实现单层的固化。通过紫外激光束,按照设计好的原件层截面,聚焦到工作槽中的陶瓷光敏树脂混合液体,逐点固化,由点及线,由线到面。通过xy方向固化成面后,通过升降台在z轴方向的移动,层层叠加完成三维打印陶瓷零件。
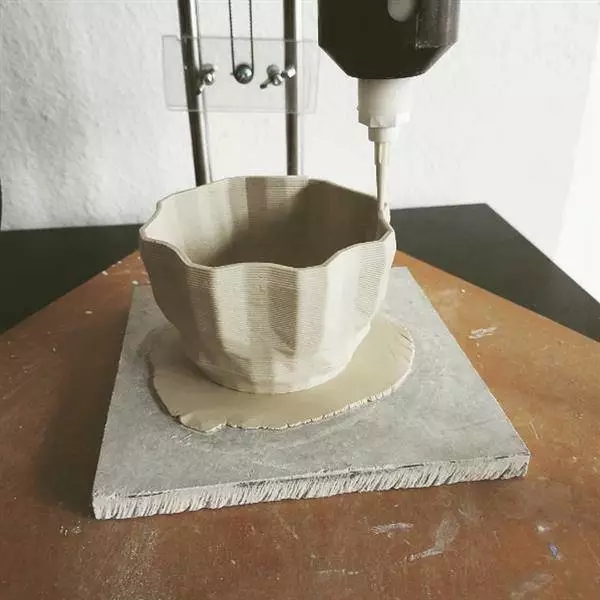
DLP技术是通过面光源的投影曝光实现单层的固化。以能在紫外光下固化的液态树脂为粘结剂,与陶瓷粉体等原料混合配制出陶瓷浆料,计算机根据每个截面的轮廓线控制紫外光照射相应区域,浆料很快固化形成一层轮廓,逐层叠加,新固化的一层粘结在前一层上,如此重复直至成型完毕。
光固化成型技术发展至今已经较为成熟,适用于制作结构复杂、精度要求高的零件,已有公司研发出光固化3D打印设备。